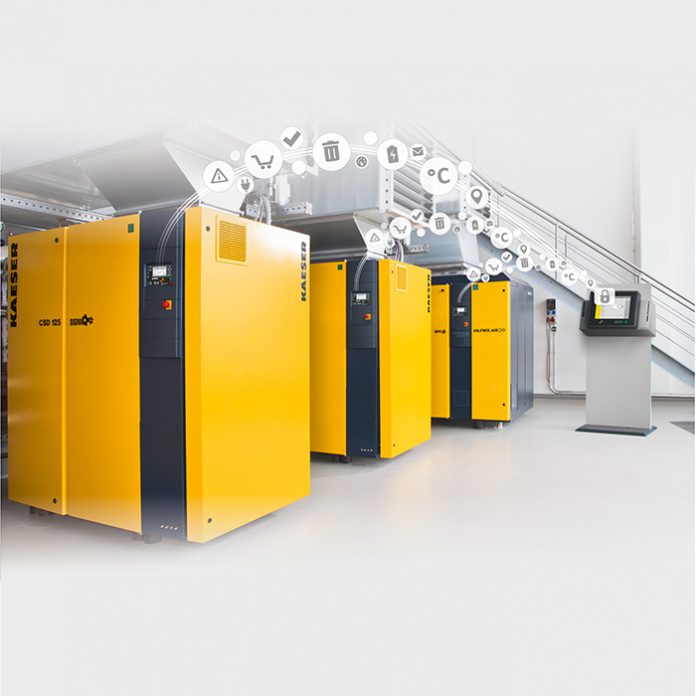
Machine-to-Machine-Communication und Industrie 4.0 stellen bei industriellen Anwendungen in der chemischen Industrie besondere Anforderungen an die Kommunikation – auch bei der Druckluftversorgung. Die Herausforderung: Die Standards stehen noch nicht fest. Moderne, anpassungsfähige Netzwerke ermöglichen allerdings schon heute eine optimale Überwachung und effiziente Steuerung der Druckluftstation und sind ausserdem fit für das, was morgen kommt.
Um eine Druckluftstation möglichst effizient zu überwachen und zu steuern, ist es nötig, so viel wie möglich über den Prozess zu wissen, der in dem System abläuft. Sensoren sind die Fühler und Augen dieses Prozesses, die das von ihnen «Gesehene» an Steuerung, übergeordnete Steuerungen und eventuell die Leittechnik weitergeben. Dadurch kann dann der Mensch die gewonnenen Daten sinnvoll nutzen.
Dreh- und Angelpunkt einer erfolgreichen Datenübermittlung sind netzwerkfähige Schnittstellen und das Netzwerk, welches die Daten übermittelt. Genau hier liegt noch die Unsicherheit. Denn soweit die Schnittstellen betroffen sind, ist in der Automatisierung von Prozessanlagen das Definieren von Standards noch in Arbeit. Viele Betreiber von Druckluftstationen haben daher abgewartet, um zu sehen, wohin die Reise geht. Dabei lassen sich schon heute durchaus sinnvolle Schritte unternehmen, um eine effiziente und zeitgemässe Druckluftversorgung zu etablieren, die darüber hinaus zukunfts- und Industrie-4.0-fähig ist. Denn es gibt bereits Systeme, die eine effiziente und Energiekosteneffiziente Druckluftversorgung bieten. Ausserdem bereiten sie gleichzeitig den Betrieb auf Industrie 4.0 vor und sind so gestaltet, dass sie auch alle kommenden Entwicklungen mittragen.
Ethernet als Standard
Ethernet und die damit verbundenen digitalen Bussysteme erfüllen in jeder Phase des Lebenszyklus einer Anlage wichtige Anforderungen der Anwender und sind der analogen Kommunikation in Bezug auf Qualität, Kosten und Geschwindigkeit deutlich überlegen. Ausserdem sind digitale Bussysteme die technologische Voraussetzung für Themen rund um Industrie 4.0. Somit steht einer sofortigen Investition und Nutzung moderner Netzwerke nichts mehr im Weg. Zum Beispiel basiert das Kaeser Sigma Network auf Ethernet. Neben Ethernet als Basis-Technologie hat das Sigma Network zusätzlich Innovationsreserven eingebaut, die kommende Entwicklungen in der Industrie berücksichtigen. Das System ist protokolloffen und kann gängige Standards der Prozesstechnik, wie zum Beispiel Modbus / Transmission Control Protocol (TCP), bereits abdecken. Auch künftige, IP-basierte Entwicklungen lassen sich in der Vernetzung prozesstechnischer Anlagen integrieren. Dies kommt dem Betreiber bei eventuellen Erweiterungen oder Neuinstallationen in der Zukunft zugute, weil es Investitionssicherheit mit sich bringt.
Grosse Datenmengen schnell übertragen
Doch zunächst einmal ist das Kaeser Sigma Network ein lokales Netzwerk innerhalb der Druckluftstation, welches eine optimale Integration der Komponenten einer Druckluftstation ermöglicht. Der weit verbreitete Protokollstandard TCP / IP – auch als Lingua Franca des Internets bekannt – bildet die Grundlage des Datenverkehrs im Sigma Network. Im Unterschied zu gängigen Feldbuslösungen wie Profibus oder CAN, die relativ langsam arbeiten, ist dieses Fast-Ethernet-Netzwerk enorm schnell, mit einer Übertragungsgeschwindigkeit von 100 Mbit / s. Diese Datenautobahn bietet eine enorme Bandbreite für Prozessdaten, welche dem künftigen Datenaufkommen im Zuge der Digitalisierung gewachsen ist.
Sigma Network bildet zusammen mit der übergeordneten Steuerung Sigma Air Manager 4.0 (SAM 4.0) eine perfekt aufeinander abgestimmte Infrastruktur und stellt Daten für künftige Services wie vorausschauende Wartung oder Energiemanagement zur Verfügung. Dies senkt die Kosten und erhöht die Betriebssicherheit und Verfügbarkeit.
Zugriff auf Betriebsdaten
Die Betriebsdaten der Druckluftstation lassen sich über eine Breitbandverbindung an das Daten Center des Systemanbieters übertragen. Dies ermöglicht eine Ferndiagnose der Druckluftversorgung durch Spezialisten und künftige Services wie vorausschauende und bedarfsorientierte Wartung. In der Kombination bietet dies dem Betreiber der Druckluftstation nicht nur eine hohe Versorgungssicherheit, sondern auch geringe Life-Cycle-Kosten. Fachleute behalten das energetische Verhalten der Druckluftstation konstant im Auge und passen es bei Bedarf an das energetische Optimum an. Zusätzlich können die Betriebsdaten ohne Weiteres in die vorhandene eigene Leittechnik eines Unternehmens eingebunden werden. Flexible Schnittstellenmodule mit den gängigen Protokollen und Technologien ermöglichen die Plug-&-Play-Anbindung vor Ort.
Moderne Webtechnologien ermöglichen einen Browser-basierten Zugang. So sind die Daten jederzeit zum Beispiel vom eigenen PC oder Laptop aus abruf- und einsehbar. Der Betreiber braucht nur die entsprechende Web-Adresse aufrufen und hat sofort eine komplette Darstellung der Station mit der aktuellen Live-Ansicht. Dadurch, dass das Netzwerk konstant alle Daten ermittelt, ist für den Betreiber ein exaktes Energiemanagement nach ISO 500001 möglich. Es lassen sich automatisch alle notwendigen, vorher ausgewählten Daten generieren, weiterleiten und auch in vorausgewählten Zyklen per E-Mail zusenden. Ebenso kann das System Vergleiche, Diagnosen und Analysen des Druckluftverbrauchs erstellen. Die Daten der Station sind über ein Jahr intern gespeichert und können zu Auswertungszwecken herangezogen werden.
Sicherheit für Netzwerk und Daten
Natürlich ist auch Datensicherheit immer ein Thema. Grundsätzlich lässt sich sagen, dass es eine 100-prozentige Sicherheit gar nicht geben kann. Aber ein System lässt sich so gestalten, dass ein hoher Grad an Sicherheit zustande kommt. Die Infrastruktur und ergänzende Massnahmen gewährleisten diese Sicherheit der Daten. In der Abstimmung zwischen Hersteller und Betreiber lässt sich so die Forderung nach Verfügbarkeit, Integrität und Vertraulichkeit einer vernetzten Infrastruktur erfüllen.
Intern arbeitet das Sigma Network mit spezifischen Adressen und bildet ein abgeschlossenes, betriebssicheres Netzwerksegment entsprechend den Empfehlungen für industrielle Steuerungssysteme (ICS), in dem nur bekannte Kommunikationsteilnehmer akzeptiert sind. Die übergeordnete Steuerung SAM 4.0 ist eine zentrale Komponente dieses Kommunikationsverbundes. Mithilfe der hier eingebauten Massnahmen findet eine datentechnische Isolation zwischen dem stationsinternen Sigma Network und den extern verbundenen Netzen statt.
Geht es nun darum, die Daten aus der Druckluftstation weiterzugeben, so ermöglicht ein definierter Übergangspunkt, Daten sicher mit externen Partnern auszutauschen. Diese trennende Instanz verhindert ein Durchgriff auf das stationsinterne Netzwerk. Die Richtung der Daten geht stets von «innen» nach «aussen». So können keine Daten von aussen ins Netzwerk fliessen, die den sicheren Betrieb stören könnten.
Fazit
Der Standard in der Prozessindustrie steht zwar noch nicht fest, aber Ethernet als Basis zeichnet sich ab. Moderne Netzwerke in der Druckluftversorgung basieren bereits darauf und sind zukunftsfähig. Sie bieten dem Anwender eine moderne, effiziente, versorgungssichere, leistungsstarke und Energiekosten-sparende Druckluftversorgung bei gleichzeitig hohem Komfort in Anwendung und Betrieb. Darüber hinaus sind sie zukunftsfähig und erweiterbar im Hinblick auf kommende Kommunikationsstandards, technische Entwicklungen, Kapazität und Übertragungsgeschwindigkeit.

Kompressoren SE.
